Key takeaways
On this page
rom its origins back in 1936, the solar panel industry rose to become one of the biggest renewable energy mainstays. It all began with the invention of the photovoltaic effect by French physicist Edmond Becquerel in 1839. While experimenting in his father's laboratory as a nineteen-year-old, he placed two electrodes in an acidic solution. The scientist exposed one of them to light, which generated voltage and current. And even though Becquerel had developed the basic principle of solar cell operation, generations passed before the creation of solar panels as we know them today.
Short history of solar cell production
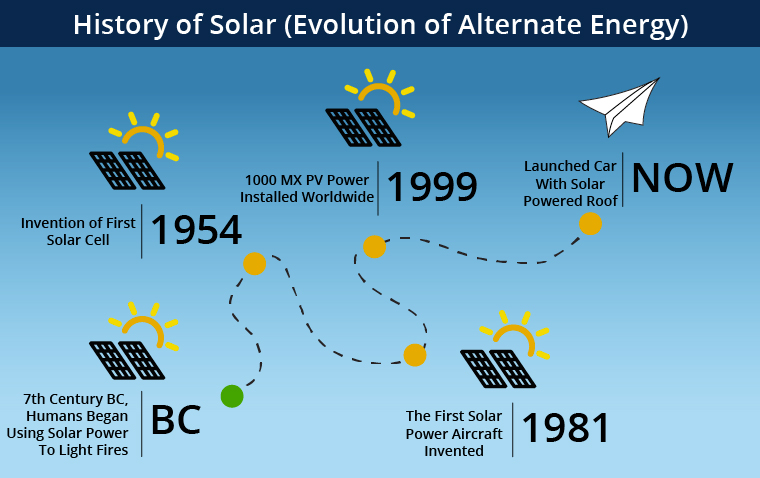
American inventor Charles Fritts fabricated the first solid-state solar cells in 1883 from selenium; he later installed the first photovoltaic system on a New York rooftop. Fritts argued that his panels would soon compete with Thomas Edison's coal-fired plants. Still, the scientific community didn't take much interest in solar panel technology, as the efficiency of photovoltaic cells at that time did not exceed 1%.
The following significant breakthrough in the solar panel industry was made in 1905 when Albert Einstein described light as a collection of discrete particles (photons). His work gave a massive impetus to the development of modern solar panel technology.
Almost 50 years later, three scientists at Bell Laboratories — Daryl Chapin, Calvin Fuller, and Gerald Pearson — announced that they had found an effective way to turn sunlight into usable energy by fabricating the first-ever silicon solar cell. The cell demonstrated a conversion efficiency of 4%; two years later, the Bell Labs scientists developed a cell with 6% efficiency.
How hot do solar panel get? Photovoltaic cells still weren’t efficient enough for commercial solar panel manufacturing. However, they found applications in the spacecraft industry. Vanguard 1, launched into space in 1958, became the first satellite to use solar panels which together generated about 1 watt of electricity.
Solar cells found the spotlight after 1973. The OPEC embargo caused an oil shock: energy prices soared, leading to fuel shortages throughout the United States. The crisis accelerated the rollout of solar energy, and solar technologies were bolstered by strong government support.
Today the total solar panel capacity in the US exceeds 130.9 gigawatts (GW), enough to power 23 million homes. And everything points to the fact that solar panels are here to stay, becoming the primary renewable energy source. Understanding how solar panels are made helps in evaluating their quality and performance.
Solar cells – the main component of a solar panel
Solar cells have evolved through time, originally fabricated from selenium and reaching only 1% efficiency, which is far from what we enjoy today. Before we look at the solar panel manufacturing process, let’s quickly recap how photovoltaic cells actually operate.
Most solar panels sold today are made from silicon – a semiconductor material found in the form of silicon dioxide in sand, clay, soil, and practically all rocks. It is the most abundant element on Earth after oxygen, making up 27.7% of the Earth's crust, which significantly increases the cost-effectiveness of solar module manufacturing.
Solar cells consist of two layers of silicon: p-type and n-type layers. To make a p-type PV cell layer, silicon is doped with boron possessing three valence electrons (versus silicon with a valence of four), which creates a deficiency of one electron – a positively charged “hole.” Meanwhile, the n-type PV cell layer is doped with phosphorus with five valence electrons bringing an extra valence electron not involved in covalent bonds, thus making the cell negatively charged.
Hence, p-type silicon has an excess of positive charge carriers, and n-type silicon has an excess of negative charge carriers. When put together, these silicon layers create the p-n junction in the place of contact, creating an internal electric field within a cell.
When sunlight strikes the surface of a solar panel, it excites the electrons within the cell, and the electric field pushes them from one side of the junction to another. This movement of electrons in one direction around the circuit within a cell creates an electric current that later flows from solar modules through a series of wires to power our homes. Understanding how solar panels are made highlights the manufacturing process and materials.
Solar panel manufacturing step-by-step
The production cycle of solar panels involves multiple stages, each requiring absolute precision and careful monitoring. Let us look at the solar panel manufacturing process more closely. Here’s a simple step-by-step walkthrough to help you understand how solar panels are made.
Silicon for solar panels is extracted
As you may already know, the raw material for solar panel production is silica. Its mining uses sand dredging or open-pit mining techniques with standard mining equipment.
Silicon is melted and purified
The collected silica sand for solar panel manufacturing is melted in an electric arc furnace at a temperature exceeding the melting point (approximately 1,400℃) and reacted with carbon to produce impure silicon, which is not yet suitable for the production of photovoltaic modules. It is further refined to manufacture either monocrystalline silicon or polycrystalline silicon - more on their differences later.
Ingots are manufactured
The resulting material for solar panels is then processed into ingots – large bars of silicon technically known as "boules." They are from 25 mm to 300 mm in diameter, usually round or rectangular depending on the solar cell technology.
Silicon wafers are cut from the ingots
Cooled ingots are sliced with a wire saw into wafers – silicon discs about 160 micrometers thick. Afterward, the wafers are polished to eliminate all the irregularities and saw marks on the surface of the future solar cells.
Solar cells are produced
Now is the time to finally make solar cells! The process starts with placing metal conductors on the surface of the wafer. These grid-like lines of copper, palladium, or silver give solar cells their characteristic texture and help the panels collect sunlight.
The next step in solar panel production is the diffusion of the dopants over the surface of the wafers to create p-type or n-type cells.
After that, the manufacturers add an anti-reflective coating to reduce the reflection losses of silicon solar cells. The most commonly used anti-reflective coatings for PV panels are titanium dioxide (TiO2), silicon oxide (SiO), or silicon nitride (Si3N4).
Solar panel is assembled
Finally, solar panels are ready to be assembled. To make a solar module, multiple photovoltaic cells are connected together in series and covered with a thin layer of glass on the front side. The back of solar panels is covered with a backsheet made of polymer materials designed to protect the electrical components of the panels from external damage. All three PV panel layers are then enclosed in an aluminum frame. And finally, the glass, cells, and backsheet are bound together with EVA (ethylene vinyl acetate) to form a solar panel.
Ready solar PV panels are tested
The ready solar panels are tested before entering the PV panel market. Manufacturers examine their performance under fixed laboratory conditions, known as Standard Test Conditions (STC). The STC for a solar panel include an irradiance of 1000 W/m2 (1 kW/m2), 25°C ambient temperature, and an air mass value of 1.5.
Another standard metric for testing solar panels is the nominal operating cell temperature (NOCT), which is closer to “real world” conditions. NOCT for photovoltaic panels implies 800W/ m² solar irradiance, an ambient temperature of 20°C, and a wind speed of 1m/ s.
Three main solar production technologies
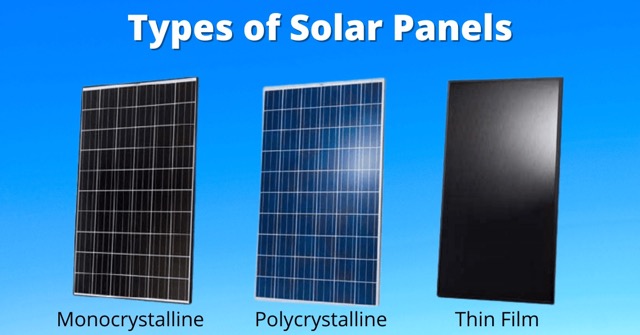
Most solar panels sold today fall into three categories: monocrystalline panels, polycrystalline panels, and thin film panels. Although they all generate electricity using the photovoltaic effect, they are pretty different from each other in terms of solar manufacturing technology. Here's a quick overview of the three most widespread solar panel types.
Monocrystalline solar
Monocrystalline solar panels consist of solar cells made from a single silicon crystal, which helps them capture more sunlight resulting in higher efficiency. These cells are manufactured using the Czochralski technique, also known as “crystal pulling.” Once the silicon is molten, a rotating small seed crystal is inserted into a melt. Then the pulling mechanism slowly withdraws the seed from the cubicle, and the melt crystallizes at the seed surface, thus forming a new portion of silicon. The seed is dipped into a melt several times to achieve the required crystal diameter. During the whole process, the manufacturers carefully control the liquid temperature and the rate of withdrawal and rotation. As a result, large cylindrical monocrystalline ingots are formed.
Polycrystalline solar
In contrast, polycrystalline silicon cells for solar panels are made of tiny grains of silicon. Polycrystalline solar panels are cheaper to manufacture but demonstrate lower efficiency due to poorer light absorption.
These cells can be produced in several ways, the most widespread being the Siemens process. Unlike monocrystal solar cells, poly-Si cells are manufactured from metallurgical-grade (MG) silicon which has to be purged of 0.5% to 1.5% of impurities it usually contains. To do this, the manufacturers create an intermediate product called trichlorosilane which is later decomposed to obtain semiconductor-grade polysilicon. The liquid silicon is later solidified in a square-shaped mold, where it acquires a granular structure and takes the form of a rectangular ingot.
Thin-film solar
While the solar panel market is currently dominated by crystalline silicon, there is one more promising PV panel option that employs an entirely different solar cell manufacturing process.
Thin-film solar cells are made by chemical vapor deposition, where a thin layer of semiconductor material is deposited on a glass, steel, or polyimide substrate. The most common semiconductors used in thin-film solar panel manufacturing are cadmium telluride (CdTe), amorphous silicon (a-Si), and copper indium gallium diselenide (CIGS).
These cells use much less semiconductor material, cutting down the PV panel manufacturing cost. Additionally, thin-film panels are flexible and don’t require assembling, which is a considerable advantage over conventional crystalline solar panels.
A Solar Panel PPA (Power Purchase Agreement) offers an attractive alternative for homeowners and businesses interested in solar energy but hesitant about the upfront costs. With a PPA, a solar provider installs and maintains solar panels on your property, and you agree to purchase the electricity generated by the panels at a fixed rate over a set term, typically 15 to 25 years. PPA agreements often include performance guarantees and maintenance services, providing peace of mind to customers. Learn more about the benefits of a Solar Panel PPA and how it can help you transition to clean, renewable energy Solar Panel PPA.
Sources:
Related





Key takeaways
Solar Panels Unveiled: Past and Present Insights
- Historical Evolution: Trace the journey from Edmond Becquerel's photovoltaic effect in 1839 to today's solar panel industry, highlighting key milestones like Charles Fritts' selenium cells and Bell Labs' silicon solar cell breakthrough.
- Solar Surge Post-1973: Witness the turning point after the 1973 OPEC oil crisis when solar energy gained momentum. Currently, the US boasts over 130.9 GW solar panel capacity, illuminating 23 million homes, solidifying solar as the top renewable energy source.
- Solar Cell Dynamics: Delve into the intricacies of solar cells, initially crafted from selenium and now predominantly silicon-based. Unravel the science behind p-type and n-type layers, exploring the internal electric fields crucial for electricity generation.
- Solar Panel Production: Uncover the meticulous solar panel manufacturing process, from silicon extraction to ingot creation, wafer slicing, solar cell production, and eventual assembly. Learn how each step contributes to the final product.
- Three Solar Panel Types: Differentiate between monocrystalline, polycrystalline, and thin-film solar panels. Understand the manufacturing techniques behind each type, highlighting efficiency, cost, and material differences.
- Efficiency Metrics: Grasp the significance of efficiency metrics in solar panels, including Standard Test Conditions (STC) and nominal operating cell temperature (NOCT). Learn how these metrics impact a solar panel's real-world performance.
This exploration uncovers the fascinating journey of solar panels, shaping the landscape of renewable energy in the USA, from historical roots to modern production techniques.