Key takeaways
On this page
ccording to the International Energy Agency (IEA), the amount of solar power capacity installed globally grew by a record 179 TWh in 2021. In its World Energy Outlook 2022, the agency predicts that the annual growth of solar will increase to more than four times its current rate, reaching 650 GW in 2030. The surge in solar adoption is primarily driven by the falling cost of photovoltaic technology, making it more affordable for households and businesses to switch to solar energy.
Although utility-scale solar power still reigns in the global solar market, residential photovoltaics is also gaining momentum. The demand for residential solar panels is on the rise as more and more homeowners are realizing how beneficial solar is. Not only does it provide a clean and renewable source of energy, but it can also save homeowners money on their monthly electricity bills.
But while the benefits of solar power are widely known, many are still in the dark about the technologies that make it possible, even though they are truly fascinating. This article will take you on a tour through solar panel manufacturing, from raw materials to a finished product, and introduce you to how solar panels are made.
Explore How Solar Panels Are Made
Silicon – the cornerstone of solar cell production
Every solar panel consists of photovoltaic cells, also called solar cells - devices that convert sunlight into electricity. PV cells can only be made from semiconductors, which are materials with a special atomic structure that allows their conductivity to be influenced by light. When the light hits the surface of a solar cell, it excites the electrons in the semiconductor, causing them to move in one direction – this is how an electric current is generated.
Examples of semiconductors include silicon, germanium, gallium arsenide, and elements found near the "metalloid staircase" on the periodic table. But of those, only silicon managed to become the go-to material for solar panel production, with over 90% of solar panels worldwide being made from silicon. So what makes it so unique?
Silicon is the most popular for several reasons. Firstly, it is the second most abundant element in the Earth's crust. This allows for producing large quantities of solar panels at a relatively low cost.
Secondly, silicon has a high efficiency rate in converting sunlight into electricity. This means that solar panels made from silicon can produce more energy than other materials.
Lastly, silicon has a long lifespan and is resistant to degradation, allowing for the production of durable and reliable solar panels. This ensures that solar panels made with silicon will continue to produce energy for many years.
Additives making solar cells even more efficient
While silicon is one of the most efficient materials for solar panels, it still has its limitations in terms of efficiency. A single-junction solar cell has a theoretical upper limit of only 32%, meaning it can only convert one-third of the light that reaches its surface into electricity. However, researchers are working to overcome this efficiency barrier by exploring the potential of additive materials. By doing so, they hope to increase the amount of light that can be converted into electricity, ultimately leading to more efficient and cost-effective solar panels.
By combining silicon with aluminum, antimony, or lead, researchers are developing multi-junction solar cells with improved energy bandgap, increasing the efficiency of PV panels. Copper, indium, gallium, and selenide are also being used in the development of advanced solar panels.
Materials used to assemble solar cells into a solar panel
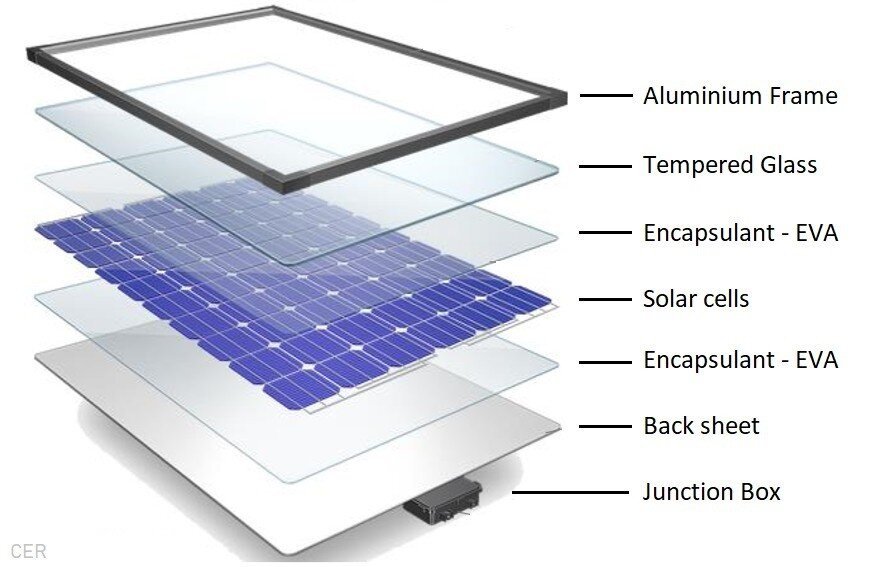
The efficiency of a solar panel relies heavily on the materials utilized in its construction.
The materials used to assemble these cells into a solar panel are crucial to its effectiveness. Glass, plastic, and metal are the most commonly utilized substances in this process.
Glass is used as the cover of the solar panel, providing a protective layer over the solar cells. It is a strong and transparent material that allows light to pass through, enabling solar panels to capture maximum sunlight. Plastic serves as a backing material protecting delicate solar cells from damage. Metal is used as the frame of the solar panel, providing structural support and allowing it to be mounted onto a roof or other surface.
How are solar panels made? The manufacturing walkthrough
Let's explore how solar panels are manufactured. This process involves several steps, which we are going to examine in detail.
Step 1: Formation of silicon ingots for solar
The production of a photovoltaic panel begins with the extraction of silicon from sand. This is typically done through a process called carbon thermal reduction, in which quartz sand is heated with carbon to extremely high temperatures, resulting in the formation of pure silicon.
Once the silicon for solar has been extracted, it is carefully purified. This is done through a series of chemical and physical processes, including the removal of any impurities or contaminants that may affect the performance of the solar panel. For photovoltaics, the purity of silicon needs to be at least 99.9999% (six nines).
The next step involves forming ingots, which are large blocks of silicon that can be easily cut and shaped into the desired form. The technology used to make the ingots depends on the solar panel type: higher-quality monocrystalline or lower-quality polycrystalline.
For monocrystalline solar panels, manufacturers use the Czochralski method, which is the growth of a single silicon crystal ingot from the molten source material. The crystal is carefully pulled and rotated to control its growth and uniformity. Fabricating the ingots used for polycrystalline solar panels, on the other hand, involves melting down multiple silicon crystals and allowing them to cool and solidify together.
Step 2: Fabrication of solar cells - constituent units of a solar panel
So how are silicon ingots turned into solar cells? The first step is to cut them into thin, circular discs known as wafers. This process is carried out using a specialized diamond or wire saw, which can cut through the hard silicon material with precision. The resulting wafers are about 160 micrometers thick.
Next, solar wafers are treated with various chemicals to create the necessary electrical properties. This process is called doping, and it involves introducing small amounts of impurities into the silicon to make a positive and negative charge.
A thin layer of aluminum or silver is deposited onto the wafer to create metal contacts on the solar cell’s surface. This layer acts as the electrical conductor, allowing the generated electricity to be collected and used. The metal contacts are typically patterned in a grid-like design.
Step 3: Solar panel assembly
The next step is solar panel assembly. It starts with the individual solar cells being soldered together to create a solar panel. Then, the panels are placed onto a backing material and sealed with a special type of adhesive. Then comes the protective covering, which helps to keep the panels safe from external impacts. This PV panel layer is typically made from solid and durable tempered glass.
All these layers of the panel are put into a metal frame, which helps to hold them in place. The panel frame is typically made from aluminum, which is both strong and lightweight, making it ideal for use in solar panels.
Thin-film solar panels: an alternative way of solar production
The steps described above apply to the production of crystalline silicon solar panels. But there are also alternative solar panel technologies, such as thin-film photovoltaics. Unlike traditional solar panels, thin-film panels are flexible and lightweight, making them ideal for vehicles, curved building facades, and curved roofs.
Thin-film solar panels are made through a process called depositing. This involves using a specialized machine to deposit layers of photovoltaic material onto a substrate, such as glass or metal. The layers are typically very thin, hence the name. The machine can deposit multiple layers at once, allowing for a high production rate. Once the layers are deposited, solar panels are heated to activate the photovoltaic material and make it able to convert sunlight into electricity.
Interested in understanding solar cell technology? Explore our article on Solar Cell Output to learn about the factors influencing the output efficiency of solar cells. Additionally, discover groundbreaking advancements in solar cell technology developed by a U.S. company for space applications in our article on U.S. Company Develops Next-Level Solar Cells for Space.
Sources:
Related





Key takeaways
Global Solar Shift
- Record Surge: In 2021, global solar capacity experienced a remarkable increase of 179 TWh.
- Future Growth: Predicted by the International Energy Agency, solar capacity is expected to quadruple to 650 GW by 2030.
Affordability Spurs Adoption
- Cost Reduction: Falling photovoltaic costs make solar energy more accessible to households and businesses.
- Rising Demand: Clean energy benefits and significant cost savings drive the increasing demand for residential solar panels.
Silicon Dominance
- Abundance and Efficiency: Over 90% of global solar panels rely on silicon due to its abundance, efficiency, and durability.
- High Conversion Efficiency: Silicon's high conversion efficiency ensures superior energy production.
Efficiency Boost with Additives
- Research Focus: Additives like aluminum, antimony, and lead are explored for enhanced solar cell efficiency.
- Multi-Junction Cells: Combinations like copper, indium, gallium, and selenide in multi-junction solar cells boost efficiency.
Critical Panel Construction
- Key Materials: Glass, plastic, and metal play pivotal roles in assembling solar cells.
- Protective Functions: Glass protects, plastic shields, and metal frames provide structural support.
Solar Panel Manufacturing Process
- Initial Steps: Silicon extraction, purification, and ingot formation are crucial initial steps.
- Cell Fabrication: Cutting ingots into wafers, doping, and adding metal contacts are part of cell fabrication.
- Assembly Process: Solar panel assembly involves soldering cells, sealing, and adding protective tempered glass covering.
Alternative Solutions
- Thin-Film Panels: Thin-film solar panels offer flexibility and lightweight solutions through depositing processes.
Understanding the solar panel production process illuminates the technology driving the renewable energy shift, emphasizing efficiency, sustainability, and cost-effectiveness.