Key takeaways
On this page
he development of solar panel technology has been a long and arduous process. It has evolved over the years, making solar energy more accessible to the masses. Since it has proven to be an environmentally friendly and cost-effective option for producing electricity, more and more homeowners choose solar panels for domestic power generation.
However not many have an idea of what are solar panels made of, how they are created, and what are the manufacturing technologies behind them. This article throws light on the production process of solar panels and gives a step-by-step walkthrough on how they are manufactured.
What are solar panels made of?
Solar cells
The first and most important component of any solar panel is a solar cell, also called a photovoltaic (PV) cell. It is an electrical device that absorbs sunlight and converts it into electricity using the photovoltaic effect.
Solar cells feature two layers of silicon: one is coated with boron (p-type) and the other one with phosphorus (n-type) When the light strikes the surface of the cell, electrons inside it start moving and cross the junction between two layers of silicon. Because of this migration of electrons, one layer becomes positively charged and the other one negatively charged, which creates an electric flow.
Solar panel frames
Metal frames are another important element of a solar panel. They hold it together and protect against adverse weather conditions. The predominant material used for panel frame manufacturing is aluminum, which can be either powder-coated or anodized.
An anodized panel frame is considered a better option as it reflects more heat, is tougher to damage, and easier to maintain. The only disadvantage of these solar frames is that they come only in silver color. Powder-coated panel frames, on the other hand, are available in a great variety of colors to perfectly match any rooftop. However, they are less scratch-resistant than anodized alternatives.
Solar panel cover glass
The solar panel sheet protects sensitive PV cells from dust, dirt, and moisture. It is usually a 3-6 millimeters layer of ultra-thin tempered glass with a rough surface, which is chemically treated to be tougher and less breakable than window glass. It can be additionally plated with an anti-reflective coating, which enhances solar transmittance of the panel.
Tab wire
Tab wire or tabbing wire is used to connect solar cells to generate the desired voltage. It is usually manufactured by rolling round copper wire into a flat ribbon.
Bus wire
The rows of tab-wired solar cells are connected in parallel by bus wires. They are always thicker and broader because they transmit the current which is much larger than the current carried by tab wires. But other than that, they are practically the same.
What makes silicon made solar panels so popular?
Silicon is the prevalent semiconductor material used in solar panel manufacturing, accounting for nearly 95% of the panels sold today.
The first factor which makes silicon made solar panels the best material for large-scale solar cell production is silicon’s high availability. It is the second most abundant element in Earth’s crust, which makes it relatively easy to reach.
In addition to this, a solar panel made of silicon is characterized by high energy efficiency. The most advanced solar cells can convert almost 40% of the sunlight they collect into electricity, and the solar conversion rate is likely to rise further. Silicon made solar panels are also valued for their reasonable cost for installing, high corrosion resistance, and non-toxic nature.
And yet, some options are poised to challenge silicon as the best material for solar. A solar panel made of perovskites is an up-and-coming viable alternative to silicon options. Perovskites are a family of materials with the same crystal structure as calcium titanium oxide. Such cells already can process over 25% of solar energy into usable energy, which makes them competitive with the best silicon solar cells. Besides, perovskite cells made solar panels cheaper and easier to produce. But they also have drawbacks, such as instability and rapid efficiency degradation.
How is a solar panel made of silicon manufactured?
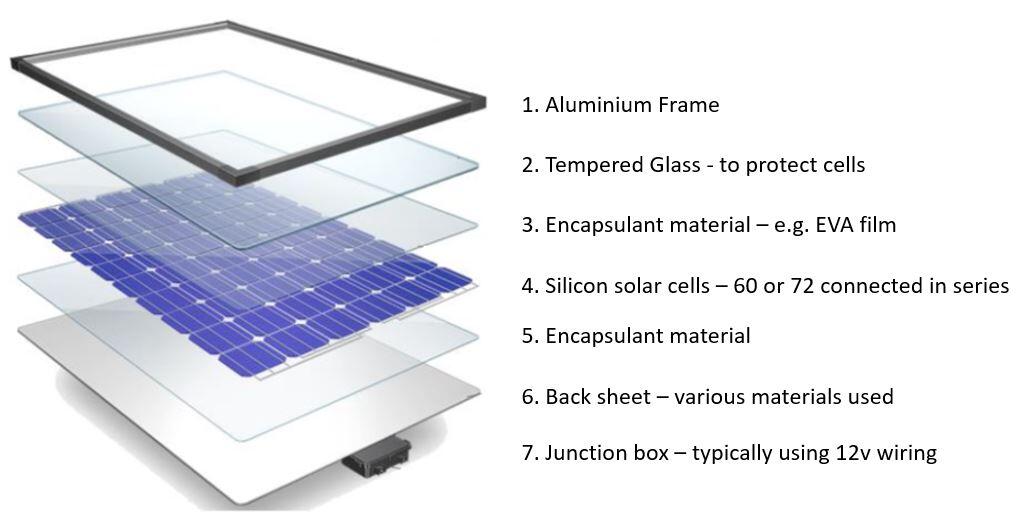
Now that we discussed what solar panels are made of, let’s go through each stage of their production.
Silicon for solar panels is extracted
The production of a solar panel made of silicon begins with mining a raw material. Silicon makes up over 27% of Earth's crust and can be found in sand, rocks, and soils. But it doesn’t exist in nature in pure form but is combined either with other materials such as oxygen. Thus, it has to be separated from other elements in the first place, which is made by heating silicon dioxide with carbon at temperatures of 1500-2000 °C.
Silicon ingots are formed
Once the material is purified, the large silicon rocks are heated them once again at high temperatures to form cylindrical ingots. To make an ingot, manufacturers put polysilicon into a container made of quartz in which it is heated and solidified in the right shape.
Ingots fall into two categories: monocrystalline and polycrystalline. Monocrystalline is created from a single crystal of silicon, which makes them more energy efficient. Polycrystalline, by contrast, is made by melting several crystals of silicon together. Solar panels that are made using monocrystalline ingots are more efficient yet more expensive.
Ingots are cut to form wafers
The next step is cutting ingots into thin discs (180 to 240 micrometers thick) using a wire saw. These discs, also called wafers, are the main structural elements of a solar panel.
Solar cells are manufactured
To make a solar cell, a wafer is supplemented with metal conductors, which create grid-like lines on the surface. These conductive contacts ensure the energy conversion of solar energy into electricity. After that, the top layer is exposed to phosphorus (a negative electrical orientation) while the bottom layer is exposed to boron (a positive electrical orientation).
A solar panel is formed
Once fabricated, solar cells are clustered into groups based on their conversion efficiency and maximum power rating. Solar cells having similar ratings are then wired together in series also called a "string" to increase the voltage of the panel. The number of solar cells in a panel is typically between 36 and 144. The two most common solar panel options on the market today are 60-cell and 72-cell. Residential solar panels usually have 60 solar cells, and panels for commercial use typically have 72 solar cells.
Joined cells are then covered with a thin layer of glass on the side that faces the sun. Then a blacksheet made of a combination of polymers is added at the bottom of the panel. It is designed to protect the solar cells from water and dust and provide electrical isolation.
After that, the manufacturers attach a junction box to the back of the panel which connects the it with solar cables. It also keeps the electricity flowing in one direction and prevents it from reverting into the panels. Finally, the panel is put into a metal frame that holds its components together.
The ready made solar panels are tested
Manufacturers test the ready made solar panels to precisely calculate what efficiency rating they have and make sure they function properly. To do this, they use Standard Test Conditions (STC) - the industry standard for the conditions under which photovoltaic solar panels are tested. These conditions imply an ambient cell temperature of 25oC, 1,000 W/m² solar irradiance, and an air mass (AM) of 1.5.
The panels are also tested under Nominal Operating Cell Temperature (NOCT) conditions, which resemble reality more accurately.
After the testing is carried out, solar panels are ready to come to the market and be purchased by homeowners and businesses.
A Solar Panel Starter Kit offers an accessible entry point into the world of solar energy. Designed for simplicity and affordability, these kits provide all the essential components needed to set up a basic solar power system. Whether you're looking to power a small cabin, RV, or backyard shed, a Solar Panel Starter Kit offers a convenient solution without the complexity of custom design. With plug-and-play functionality and scalable options, these kits empower individuals to start generating clean, renewable energy with ease. Learning how a solar panel is made provides insights into the manufacturing process and materials used.
Related





Key takeaways
Sustainable Solar Panel Production: A Snapshot
- Sun-Powered Alchemy: Silicon-based photovoltaic cells convert sunlight into electricity through boron and phosphorus layers.
- Metal Fortification: Aluminum frames shield panels from elements, ensuring enduring strength.
- Guardian Glass: Ultra-thin tempered glass layers protect solar cells, enhancing durability and solar transmittance.
- Wired Efficiency: Tab and bus wires manage current flow, facilitating smooth energy transmission.
- Silicon Sovereignty: Silicon dominates panels for its abundance, efficiency, and corrosion resistance.
- Beyond Silicon: Perovskite panels challenge silicon's dominance with over 25% energy conversion.
- Panel Genesis: The journey from silicon extraction to functional panels involves purification, ingot formation, and wafer cutting.
- Efficiency Amplified: Metal conductors enhance energy conversion through grid-like patterns.
- Power Stringing: Solar cells unite to elevate voltage and receive protective layers for resilience.
- Rigorous Assurance: Panels undergo testing to ensure reliable and efficient clean energy production.